To cope with power performance and power consumption in automobile heating seat covers, several issues and techniques are typically applied:
1.Efficient Heating Element Design: Engineers meticulously select and optimize substances for the heating elements, that specialize in high conductivity and coffee resistance to decorate efficiency.
Innovative element configurations, such as uniform distribution and precise patterning, are hired to maximise warmness transfer across the seat surface.
2.Temperature Control Systems: Integration of advanced temperature control systems, which includes PID (Proportional-Integral-Derivative) controllers, guarantees particular law of heat output.
Incorporation of sensors, such as thermocouples or thermistors, permits real-time tracking of seat temperature, allowing the machine to adapt and preserve strength as needed.
3.Variable Heat Settings: Implementation of a multi-degree heating device lets in users to customize the warmth stage primarily based on private preferences and environmental situations.
Clear person interfaces, possibly through virtual displays or touch controls, facilitate smooth adjustment of heat settings.
4.Auto-Shutoff Features: Inclusion of computerized shutoff mechanisms based on time or temperature thresholds prevents non-stop operation, keeping strength and enhancing safety.
Smart algorithms ensure that the shutoff mechanism responds accurately to numerous conditions, minimizing power wastage.
5.Energy-Efficient Materials: Selection of seat cowl materials with excessive thermal retention abilties minimizes heat loss, selling power efficiency.
Integration of insulating layers, in all likelihood the use of superior aerogel or foam technology, contributes to maintaining a snug temperature with minimal strength input.
6.Low-Standby Power Mode: Development of a low-energy standby mode guarantees that the seat cowl consumes minimum power whilst not actively heating.
Automated transition into standby mode at some stage in periods of inactiveness similarly optimizes energy utilization.
7.Integration with Vehicle Systems: Coordination with the vehicle's electric architecture permits the seat covers to synchronize their operation with the automobile's running status.
Power management protocols ensure that electricity consumption aligns with the to be had electric capacity of the car without compromising other crucial features.
8.Energy Harvesting Technologies: Exploration of technologies including thermoelectric mills or piezoelectric materials permits the conversion of waste heat or opportunity power sources into usable electric power.
Integration of power harvesting mechanisms adds a sustainable measurement to the heating seat cover's electricity supply.
9.User Education: Inclusion of precise user manuals or online guides educates users on optimizing power consumption based on climate conditions and personal options.
Clear communique approximately the relationship among warmness settings and power utilization fosters responsible and strength-green use.
10.Continuous Research and Development: Ongoing studies into rising materials, heating technology, and electricity-efficient design practices guarantees that the heating seat covers continue to be at the vanguard of technological advancements.
Collaboration with research institutions and enterprise partners allows the mixing of contemporary improvements into future product iterations.
Car seat cushion seat pad seat cover
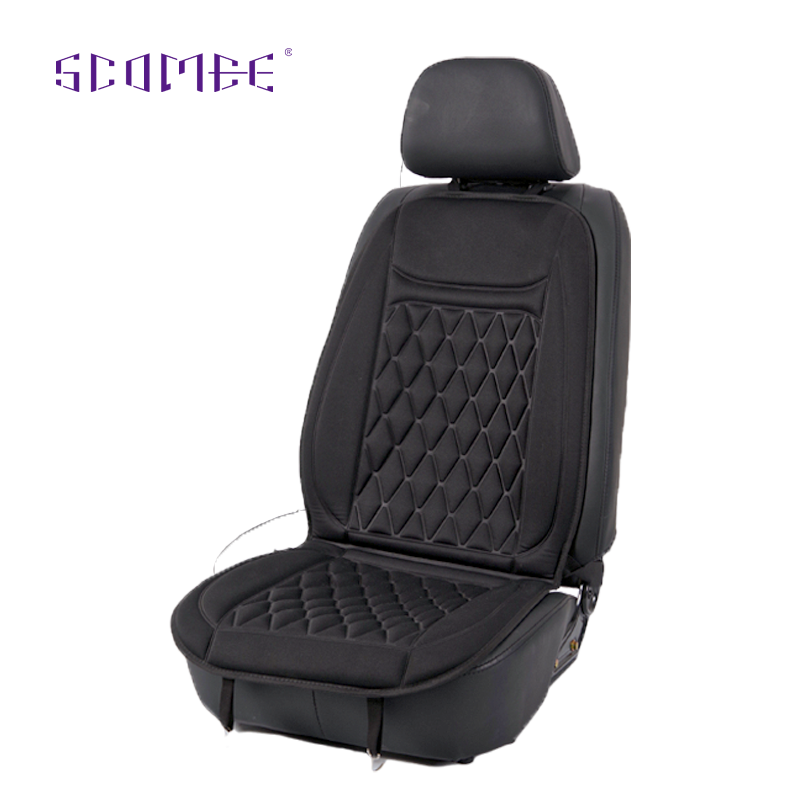
Car seat cushion seat pad seat cover
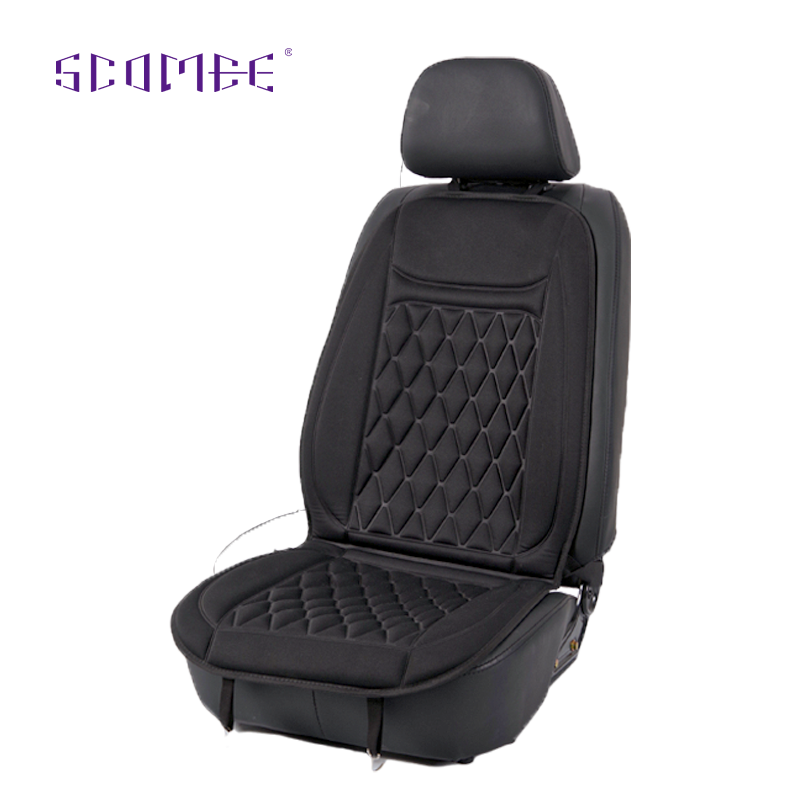